
Drilling directionally with a downhole motor requires occasionally stopping rotation of the drill pipe and "sliding" the pipe through the channel as the motor cuts a curved path. Coupled with the development of measurement while drilling tools (using mud pulse telemetry, networked or wired pipe or electromagnetism (EM) telemetry, which allows tools down hole to send directional data back to the surface without disturbing drilling operations), directional drilling became easier.Ĭertain profiles cannot be easily drilled while the drill pipe is rotating. A piece of bent pipe (a "bent sub") between the stationary drill pipe and the top of the motor allowed the direction of the wellbore to be changed without needing to pull all the drill pipe out and place another whipstock. These allowed the drill bit to continue rotating at the cutting face at the bottom of the hole, while most of the drill pipe was held stationary. The next major advance was in the 1970s, when downhole drilling motors (aka mud motors, driven by the hydraulic power of drilling mud circulated down the drill string) became common. Ĭombined, these survey tools and BHA designs made directional drilling possible, but it was perceived as arcane. In a May, 1934, Popular Science Monthly article, it was stated that "Only a handful of men in the world have the strange power to make a bit, rotating a mile below ground at the end of a steel drill pipe, snake its way in a curve or around a dog-leg angle, to reach a desired objective." Eastman Whipstock, Inc., would become the world's largest directional company in 1973. This capacity to quickly drill multiple relief wells and relieve the enormous gas pressure was critical to extinguishing the Conroe fire.
#Rem directional drilling series#
The innovation allowed rapid drilling of a series of slanted wells. He had started his company in 1931 when he mated a drilling rig to a truck and a power take-off assembly.
#Rem directional drilling portable#
Failing had recently patented a portable drilling truck. Hines of Long Beach, California, became pioneers in directional drilling when they and George Failing of Enid, Oklahoma, saved the Conroe, Texas, oil field. Counter-experience had also given early directional drillers ("DD's") principles of BHA design and drilling practice that would help bring a crooked hole nearer the vertical. Prior experience with rotary drilling had established several principles for the configuration of drilling equipment down hole ("bottom hole assembly" or "BHA") that would be prone to "drilling crooked hole" (i.e., initial accidental deviations from the vertical would be increased). A series of consecutive surveys are needed to track the progress and location of a wellbore. These three components combined are referred to as a "survey". Three components are measured at any given point in a wellbore in order to determine its position: the depth of the point along the course of the borehole (measured depth), the inclination at the point, and the magnetic azimuth at the point. Sperry did this under contract to Sun Oil (which was involved in a lawsuit as described above), and a spin-off company " Sperry Sun" was formed, which brand continues to this day, absorbed into Halliburton. The next advance was in the modification of small gyroscopic compasses by the Sperry Corporation, which was making similar compasses for aeronautical navigation. In certain circumstances, magnetic fields could be used, but would be influenced by metalwork used inside wellbores, as well as the metalwork used in drilling equipment.
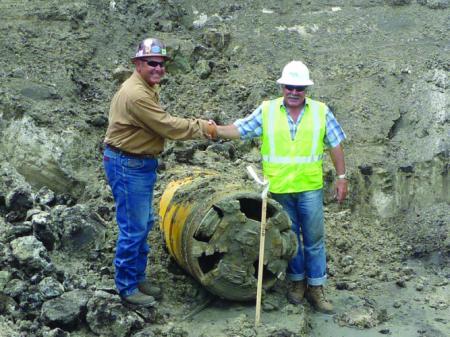
Measuring the azimuth (direction with respect to the geographic grid in which the wellbore was running from the vertical), however, was more difficult. Measuring the inclination of a wellbore (its deviation from the vertical) is comparatively simple, requiring only a pendulum. Horizontal directional drill rigs are developing towards large-scale, micro-miniaturization, mechanical automation, hard stratum working, exceeding length and depth oriented monitored drilling.

Initially, proxy evidence such as production changes in other wells was accepted, but such cases fueled the development of small diameter tools capable of surveying wells during drilling. This realization was quite slow, and did not really grasp the attention of the oil industry until the late 1920s when there were several lawsuits alleging that wells drilled from a rig on one property had crossed the boundary and were penetrating a reservoir on an adjacent property. Probably, the first requirement was the realization that oil wells, or water wells, do not necessarily need to be vertical.

Many prerequisites enabled this suite of technologies to become productive.
